Which Retort Type Is The Best? The Ultimate Guide to Selecting the Right Retort
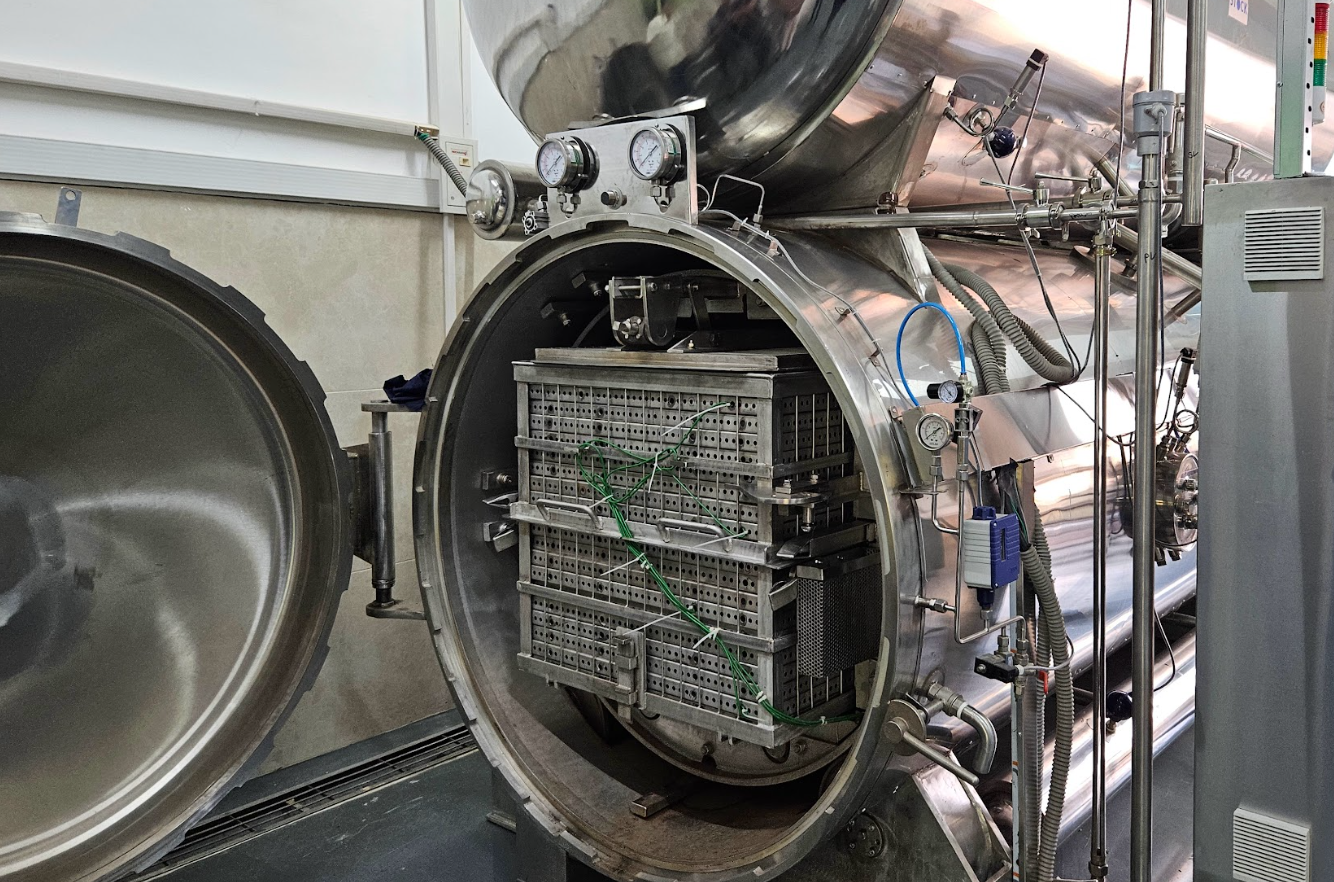
It is impossible to select a single process that it is the optimal solution for every product and container type.In the world of food processing and preservation, choosing the right retort process for your product is a critical decision that can significantly impact the quality, efficiency, and overall success of your operation. While there is no one-size-fits-all solution, understanding the distinct advantages and disadvantages of different retort processes is essential for making an informed choice. In this article, we delve into various retort types and their pros and cons to help you navigate this complex decision-making process.
Steam/Air Process: A Trusted Choice for Semi-Rigid and Pouch Containers
The steam/air process has gained widespread popularity, particularly in the processing of semi-rigid and pouch containers. This method is particularly favored in sectors such as pet food, where stand-up pouches are prevalent. One of the key strengths of the steam/air process lies in its ability to provide consistent heating across all pouch positions within the retort basket. This three-dimensional heating medium ensures uniform come-up times, regardless of pouch placement.
The direct application of energy to the product results in rapid cycle times, making it an efficient choice. Steam's greater energy availability compared to water-based methods contributes to utility savings and increased output. Furthermore, the absence of energy loss through indirect heat exchangers further enhances its efficiency.
A critical component of the steam/air process is the recirculation fan, which plays a vital role in maintaining its effectiveness. Retort manufacturers incorporate safeguards for fan operation to ensure optimal rotation and load management. Additionally, the steam process is less invasive to containers with sensitive gas barrier laminates, making it preferable in such scenarios.
Steam/Spray Process: Achieving Balanced Distribution
The steam/spray process is valued for its ability to provide effective distribution during the critical come-up phase. This method involves spraying atomized water or steam onto the containers, ensuring that heat is evenly distributed. However, there are some intricacies to consider.
One vital factor in the steam/spray process is maintaining the appropriate pressure on each nozzle to achieve optimal atomization. Proper atomization ensures that the water or steam is finely dispersed, promoting uniform heating. However, this demands careful regulation and monitoring.
Flat containers, such as trays and pouches, present a unique challenge known as the "umbrella effect." During come-up and hold stages, these flat packs can be shielded from the atomized environment due to the containers above them inhibiting the flow. Even when side sprays are employed, achieving good penetration can be challenging, especially if the layers of trays or pouches are tightly packed.
Another critical consideration is the maintenance of the spray nozzles. Ensuring that nozzles remain free from scale or other particulates is essential for the process's effectiveness. However, addressing nozzle blockages can be a complex task, often requiring entry into the retort to physically remove the affected nozzles.
Cascading Water Process: A Penetrating Solution
The cascading water process is highly effective when it comes to penetrating densely packed baskets of rigid containers, such as glass or cans. In this method, water is allowed to flow over the containers, trickling down from the top and effectively distributing heat. This vertical flow enables water to permeate between containers, ensuring thorough thermal distribution.
However, similar to the steam/spray process, certain considerations arise, particularly when dealing with pouches or flat containers. The umbrella effect, though mitigated to some extent with side sprays, remains a concern.
To overcome the challenges associated with the umbrella effect, many experts turn to rotating retorts. By employing rotating retorts, containers can turn end-over-end, allowing water to penetrate more easily and effectively reach all surfaces.
Balancing Efficiency and Time: Factors to Consider
Both the steam/spray and cascading water processes have their advantages and challenges. The water spray process, while achieving balanced distribution, often requires longer heating times compared to a steam retort. This is due to the need to heat the water prior to spraying it onto the containers or during the spraying process, especially if the product is cold-filled. Additionally, the heat loss throughout the exchanger should be factored in when calculating steam requirements.
On the other hand, the cascading water process is known for its remarkable penetration capabilities, particularly in tightly packed baskets of rigid containers. The vertical flow of water is its strength, allowing for excellent thermal distribution. However, it's crucial to consider potential challenges, especially when processing pouches or flat containers, and explore solutions like rotating retorts to optimize results.
Water Immersion Retorts: Gentle Heating and Considerations
Delicate Heating with Water Immersion
The water immersion process is widely regarded as an excellent method for achieving gentle and controlled heating. It is particularly well-suited for products and containers that require precise temperature management. What sets this process apart is its ability to offer support to containers, especially in heavy loads. The buoyancy of water provides an additional layer of support, helping distribute the weight more evenly across containers.
One of the key advantages of the water immersion process is its effectiveness in achieving uniform heating. The surrounding water ensures that heat is evenly distributed, reducing the risk of localized overheating. This is especially important when dealing with sensitive products that can be adversely affected by temperature fluctuations.
Balancing Benefits and Process Times
While water immersion brings valuable benefits, it's important to consider the trade-offs that come with the process. One significant drawback is the slower process times associated with heating a large body of water. The time it takes for the water to reach the desired temperature can extend the overall processing time, impacting production efficiency.
Challenges with Seal Qualities and Contamination
One of the notable challenges associated with water immersion retorts is the issue of seal qualities, especially in the case of semi-rigid and pouch containers. These containers often have seal imperfections, and during the immersion process, there's a risk of contaminated water transferring from one batch to another through "leakers." This can lead to multiple complications, including discoloration of white plastics, sticky residues on packs, and water migration through seals.
The presence of water in the immersion process can cause these issues due to its prolonged contact with the containers. This becomes particularly relevant when considering low-temperature pasteurization, where maintaining the integrity of the seals is crucial for product safety.
Conclusion
The process of selecting the right retort involves a delicate balancing act. It's about aligning the unique characteristics of your products and containers with the strengths of a particular retort type. The steam/air process shines in its efficiency for semi-rigid and pouch containers, offering uniform heating and energy savings. The steam/spray process excels in achieving distribution but requires careful pressure regulation and addresses challenges like the umbrella effect. Cascading water impressively penetrates rigid containers, and while it necessitates longer heating times, solutions like rotating retorts can enhance its performance. Water immersion, with its gentle and controlled heating, holds promise for delicate products. The buoyancy it provides and the uniform heat distribution it ensures are valuable attributes. However, it's essential to consider the slower process times and the potential challenges with seal qualities and contamination. In the end, the ultimate guide to selecting the right retort type revolves around your specific needs.